현대차, 탄소배출 감소시키는 ‘저온 경화 도장 기술’ 개발... 도장라인 에너지 40% 절감
기존 140℃에서 20분 경화한 것을 90℃ 20분으로 줄이는 도료와 공법 개발
현대차 국내외 모든 공장에 기술 적용하면 연간 CO2 1만6000여t 절감 예상
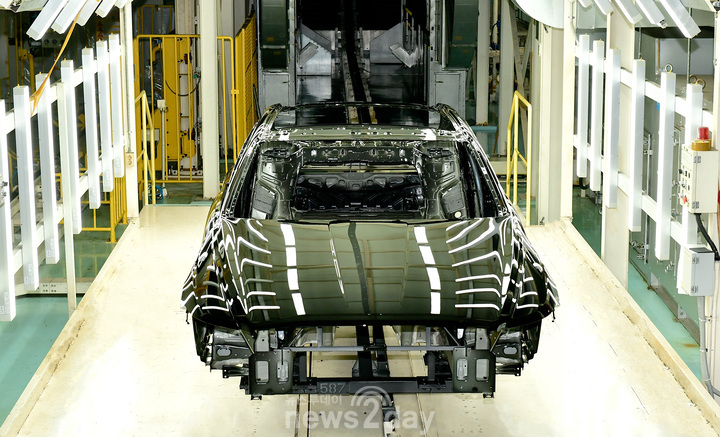
[뉴스투데이=남지완 기자] 현대차는 기존 140℃에서 20분 동안 이뤄지던 상도 경화 공정을 90℃에서 20분 동안 진행하면서도 같은 도장 품질을 유지하는 도료 기술을 개발했다고 30일 밝혔다. 이를 통해 도장 공장에서 에너지 소비를 획기적으로 줄여 탄소배출 저감효과를 극대화할 수 있을 것으로 보인다.
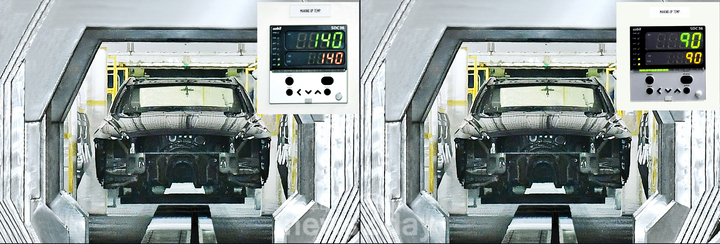
자동차 도장 공정은 크게 전처리, 하도도장, 중도도장, 상도도장 등 네 단계를 거친다. 이 과정에서 고온 처리를 통해 입혀진 도료를 단단하게 굳히는 공정을 ‘경화 공정’이라고 한다. 즉 이번에 신기술이 적용되는 분야는 상도도장 및 경화 공정이 진행된 단계라고 볼 수 있다.
기존 도료에는 약 140℃ 이상에서만 경화되는 멜라민(유기 화합물의 일종)이 함유돼 있지만 현대차가 새로 개발한 도료에는 멜라민 대신 90℃ 이상에서 경화되는 이소시아네이트(유기 화합물 일종) 성분을 적용했다. 50℃나 더 낮은 온도에서 경화되는 새로운 도료를 활용해 온도를 과도하게 높일 필요가 없어 생산과정에서의 에너지 소모를 크게 절감할 수 있게 된다.
실제로 도장 공정은 자동차 제조 공정 가운데 가장 많은 에너지(약 43%)를 사용하고 그에 따른 탄소 배출도 가장 많은 공정으로 꼽힌다. 이번 도료 기술이 상용화되면 이 부문에서 탄소 배출과 가스 사용량을 각각 40%가량 절감할 수 있을 것으로 예상된다.
특히 이 기술을 국내외 모든 현대차 공장에 적용하면 한 해 동안 자동차 제조 공정 중 배출되는 이산화탄소 가운데 1만6000여t을 저감할 수 있다.
저온 경화 기술은 탄소 저감뿐만 아니라 도장 품질 향상에도 큰 효과를 도모할 수 있다. 기존 고온 경화 공정에는 차체와 재질이 다른 플라스틱 범퍼나 휀더(자동차 바퀴를 감싸고 있는 부품) 등은 적용하기 어려워 협력사에서 도장된 채로 받아 조립했다. 그러나 저온 경화 공정을 적용하면 복합재로 이뤄진 부품도 한 번에 도장하고 경화할 수 있다.
현대차는 울산 5공장에 이 기술을 시범 적용해 제네시스 G80 차량을 시험적으로 생산했으며 운행 및 모니터링을 지속적으로 하면서 기술의 본격 적용 가능성을 평가할 예정이다.
현대차 관계자는 “이번에 공개한 저온 경화 기술은 현대차가 단순히 차량을 판매한다는 개념을 넘어 차량 생산 단계에서부터 만들어낼 수 있는 가치를 고려한 기술이라는 점에서 의의가 있다”며 “도장 공정에서 에너지 소모를 획기적으로 저감하는 기술 개발을 통해 현대차의 2045년 탄소중립 목표에 한 발 다가갈 수 있을 것”이라고 말했다.
댓글 (0)
- 띄어 쓰기를 포함하여 250자 이내로 써주세요.
- 건전한 토론문화를 위해, 타인에게 불쾌감을 주는 욕설/비방/허위/명예훼손/도배 등의 댓글은 표시가 제한됩니다.